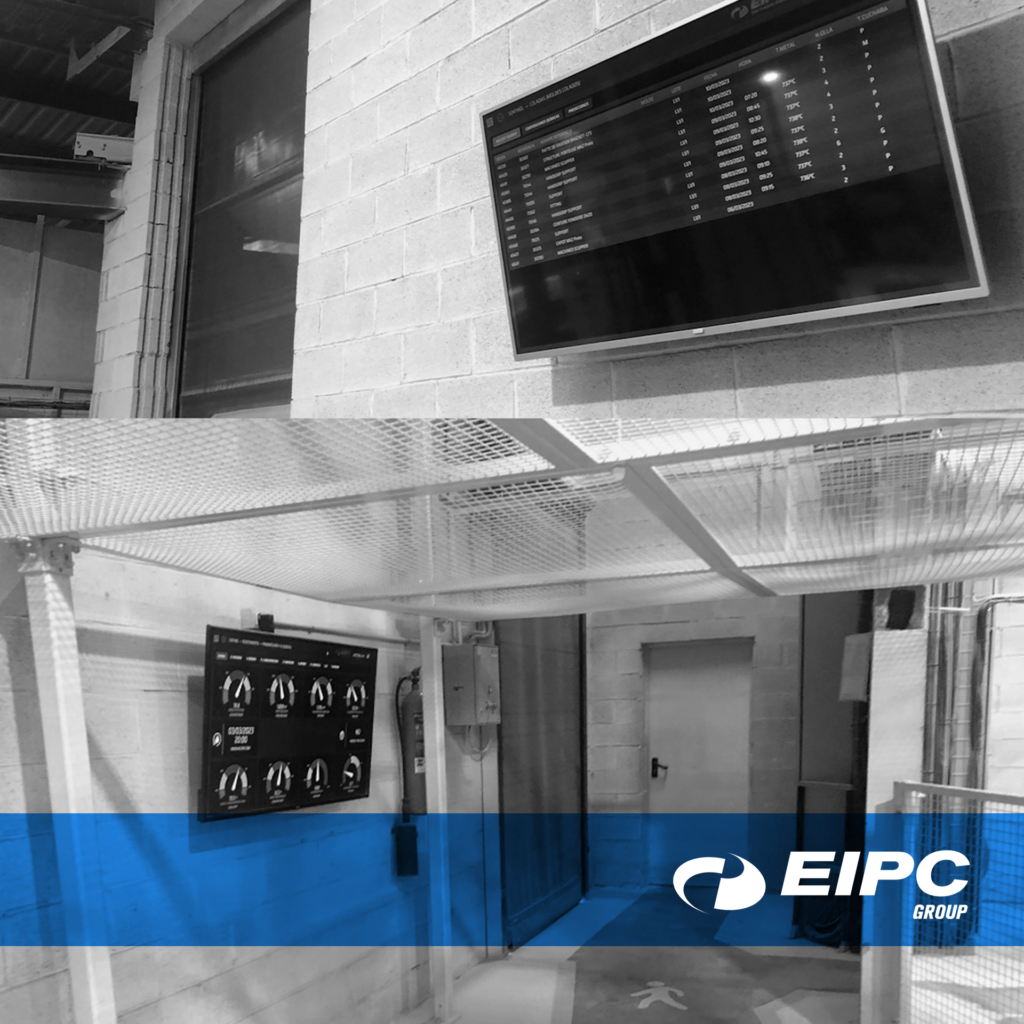
ESTUDIO: Desarrollo de gemelo un digital basado en inteligencia artificial para la reducción en la tasa de rechazo y la mejora de las propiedades mecánicas en una planta de microfusión.
Por Javier Nieves ,David Garcia, Jorge Angulo-Pines, Fernando Santos y Pedro Pablo Rodriguez
El proceso de fabricación llevado a cabo en la industria de la fundición a cera perdida sufre problemas similares a los de otros procesos de producción. Además, las elevadas exigencias de los clientes y de las industrias que requieren estas piezas obligan a cumplir altos niveles de calidad. Si no se alcanzan dichos requisitos, se produce el rechazo de las piezas fabricadas. Por ello, dada la revolución tecnológica actual (es decir, la Industria 4.0) y las posibilidades que ofrecen herramientas como los gemelos digitales y la inteligencia artificial, es posible trabajar en la generación de sistemas inteligentes que puedan reducir e incluso evitar estos problemas.
Este estudio propone la implementación de un gemelo digital basado en inteligencia artificial (IA) para reducir defectos en las piezas fabricadas y mejorar sus propiedades mecánicas. Se busca predecir y prevenir problemas antes de que ocurran, mediante la digitalización del proceso y la integración de un sistema de recomendación para corregir desviaciones. En este contexto, esta investigación aborda dos de los defectos más críticos:
- La porosidad
- Las propiedades mecánicas
El enfoque se basa en los principios de la Industria 4.0, utilizando herramientas como aprendizaje automático, sistemas de simulación y análisis predictivo para optimizar la fabricación. En concreto, este trabajo se centra en el análisis del proceso de fabricación (definición, extracción de KPIs, captura, distribución y visualización), la creación de un sistema base para la gestión integral de la optimización del proceso y los experimentos desarrollados para determinar el mejor método para realizar predicciones.
En primer lugar, se trabajó en la mejora de la digitalización y la representación de la realidad en un entorno digital. Se siguió un plan de análisis de datos que incluyó:
- Identificación de datos disponibles y de aquellos que, aunque inicialmente no estuvieran accesibles, podrían digitalizarse y extraerse posteriormente.
- Auditoría del estado de cada área y sus variables.
- Estudio del impacto y la prioridad de las áreas y sus respectivas variables.
- Creación de un repositorio centralizado de datos para almacenar la información capturada, utilizando un sistema basado en agentes como PDManager.
Posteriormente, estos datos debían ser utilizados eficientemente. Se comenzó con la creación de un gemelo digital de bajo nivel de madurez, enfocado en la visualización y monitoreo remoto. Más adelante, el gemelo digital evolucionó a un nivel de madurez superior, pasando de un enfoque reactivo a uno proactivo. En esta nueva etapa, se integraron tareas de simulación y optimización, utilizando aprendizaje automático supervisado para realizar predicciones.
Finalmente, basado en los datos recolectados y las predicciones, se diseñó un sistema que propone acciones correctivas en tiempo real para optimizar el proceso.
Para leer en estudio completo , descargar AQUÍ.
- Etiquetas de Post:
- IA
- industria digital
- investigación