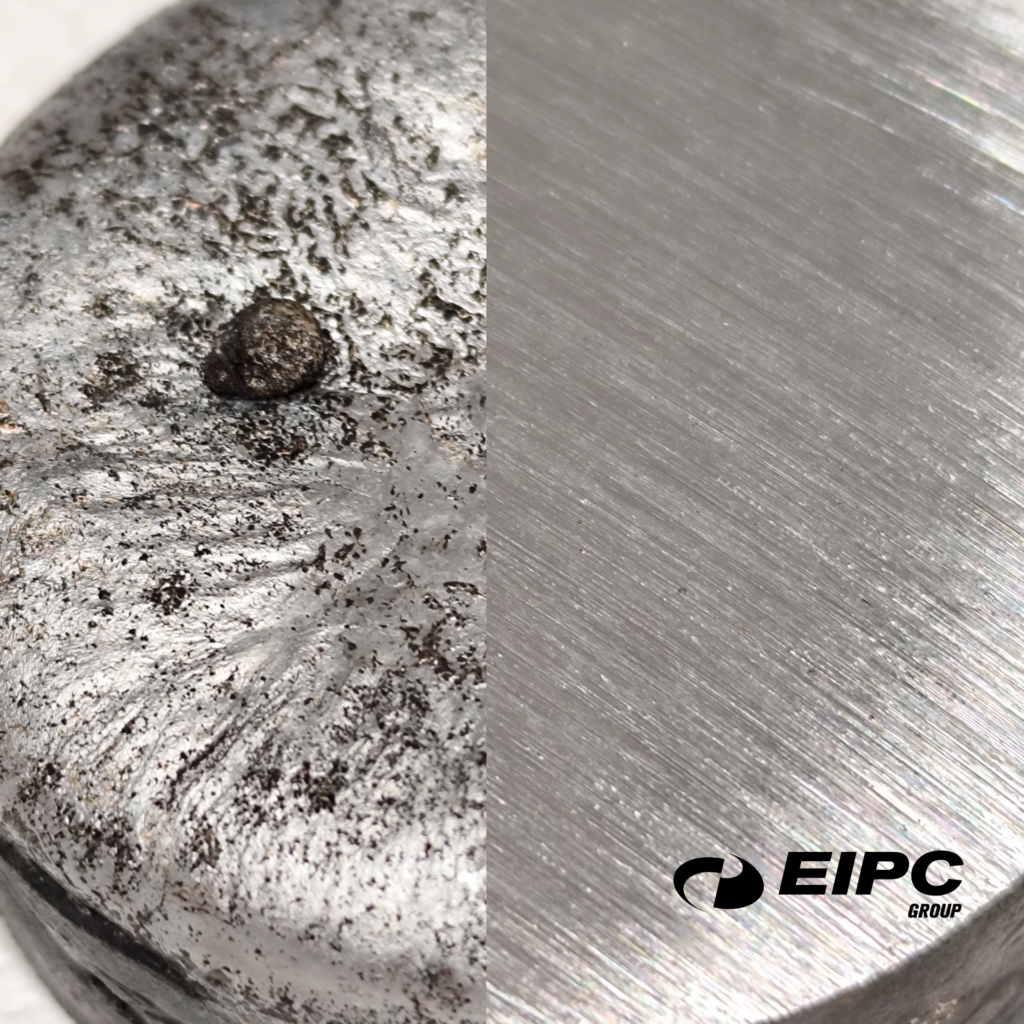
The solidification process in the investment casting industry: milestones, key factors and main challenges
Lost-wax casting, also known as investment casting or precision casting, is an ancient manufacturing technique that has evolved into a high-precision process used in a variety of industries, from aerospace to jewellery. At the heart of this metal transformation process are the phenomena of solidification and shrinkage, the understanding and control of which are fundamental to the production of high quality parts.
We will focus on the critical aspects of solidification and shrinkage compensation in the casting process. We will look at the initiation of solidification, the formation of the crystal structure, methods of solidification control, and strategies for handling shrinkage and shrinkage compensation.
Fundamentals of the metal solidification process in the lost-wax casting industry
The manufacture of a component using the lost-wax casting process begins with the creation of a wax pattern that is an exact replica of the desired final part. This pattern is coated with a refractory ceramic material which, when hardened, forms a precise mould. The wax is melted and removed from the mould, leaving a cavity which is then filled with molten metal.
The solidification process in investment casting is a key stage in the shaping of the part, as it directly influences the final quality, microstructure and mechanical properties of the part. Solidification involves the transition of the molten metal from a liquid to a solid state inside the ceramic mould, therefore it is a thermal process in which the molten metal loses heat and starts to crystallise.
As the metal cools, the atoms in the liquid phase begin to organise themselves into a crystalline structure, marking the transformation from liquid to solid. This transformation depends on several factors, including the type of metal alloy, the geometry of the mould and the cooling rate.
ALLOY TYPE
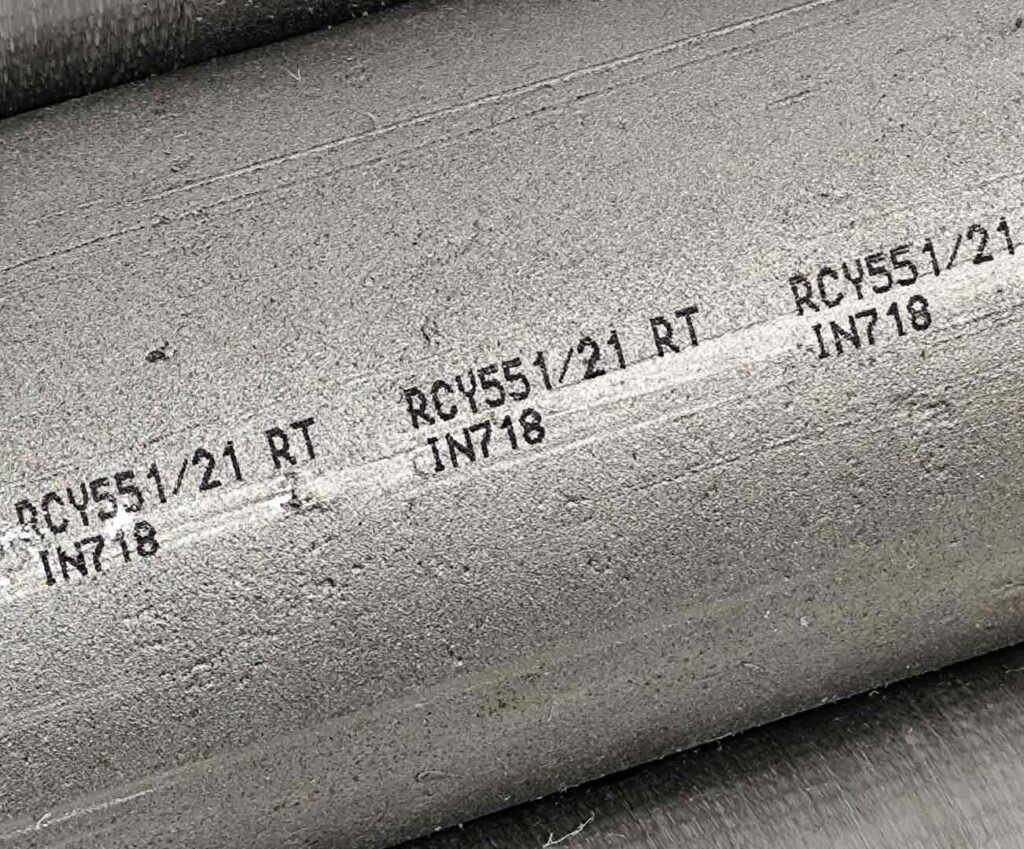
INCO 718 alloy ingot detail
The choice of metal alloy plays a crucial role in the solidification process. Different alloys have different melting and freezing points, thermal conductivities and tendencies to form specific grain structures. Each material has a unique solidification profile that influences its behaviour during cooling and crystallisation. The most common metals used in investment casting include: Aluminium alloys, Steel alloys and Super alloys mainly used in aerospace applications due to their ability to withstand extreme temperatures.
MOULD GEOMETRY
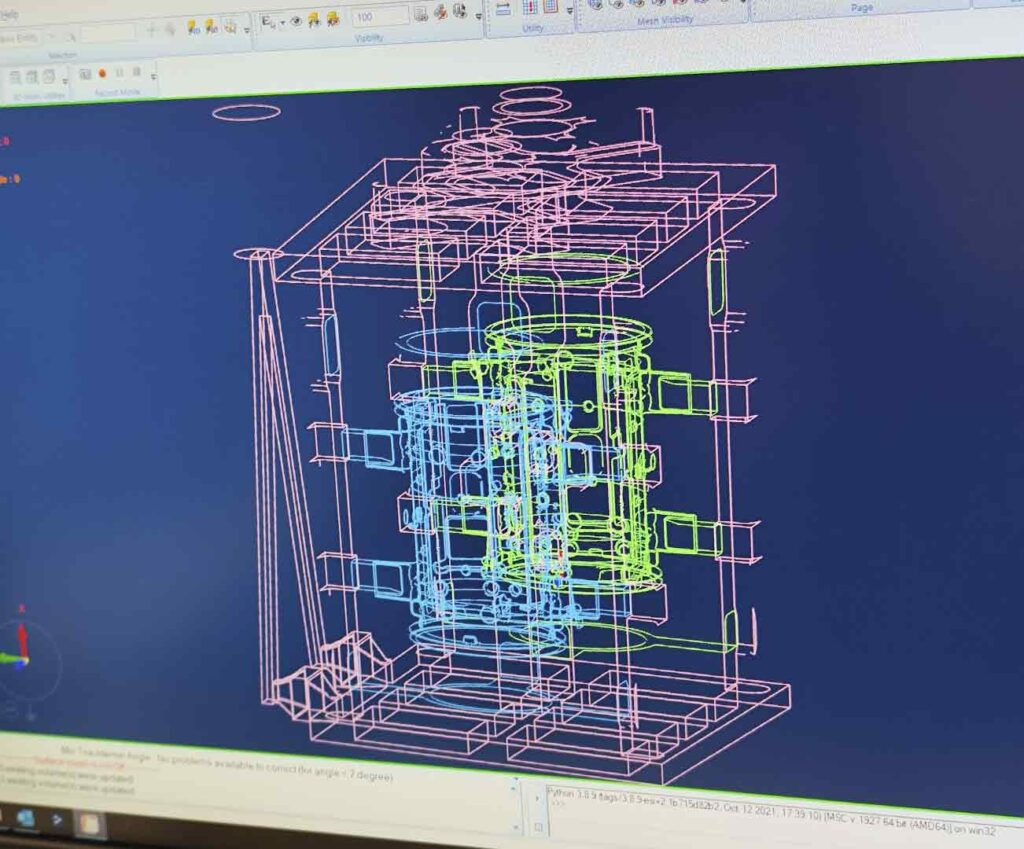
Mould design for the production of the wax positive part
The design of the ceramic mould directly affects the way the molten metal flows and solidifies within it. Key considerations include:
- Wall Thickness: The thickness of the mould walls impacts the rate at which the metal cools. Thicker walls generally slow cooling, while thinner walls tend to cause faster cooling.
- Mould Materials: The composition of the ceramic mould material influences its thermal properties. High thermal conductivity in the mould material can lead to faster cooling, which affects the solidification rate and the resulting microstructure.
- Cast Geometry: Complex geometries can create regions where the metal cools unevenly, leading to localised shrinkage defects or incomplete solidification.
COOLING RATE
The rate at which the molten metal cools and solidifies is crucial to the outcome of the casting, as defects such as porosity or shrinkage can occur if the process is not properly controlled.
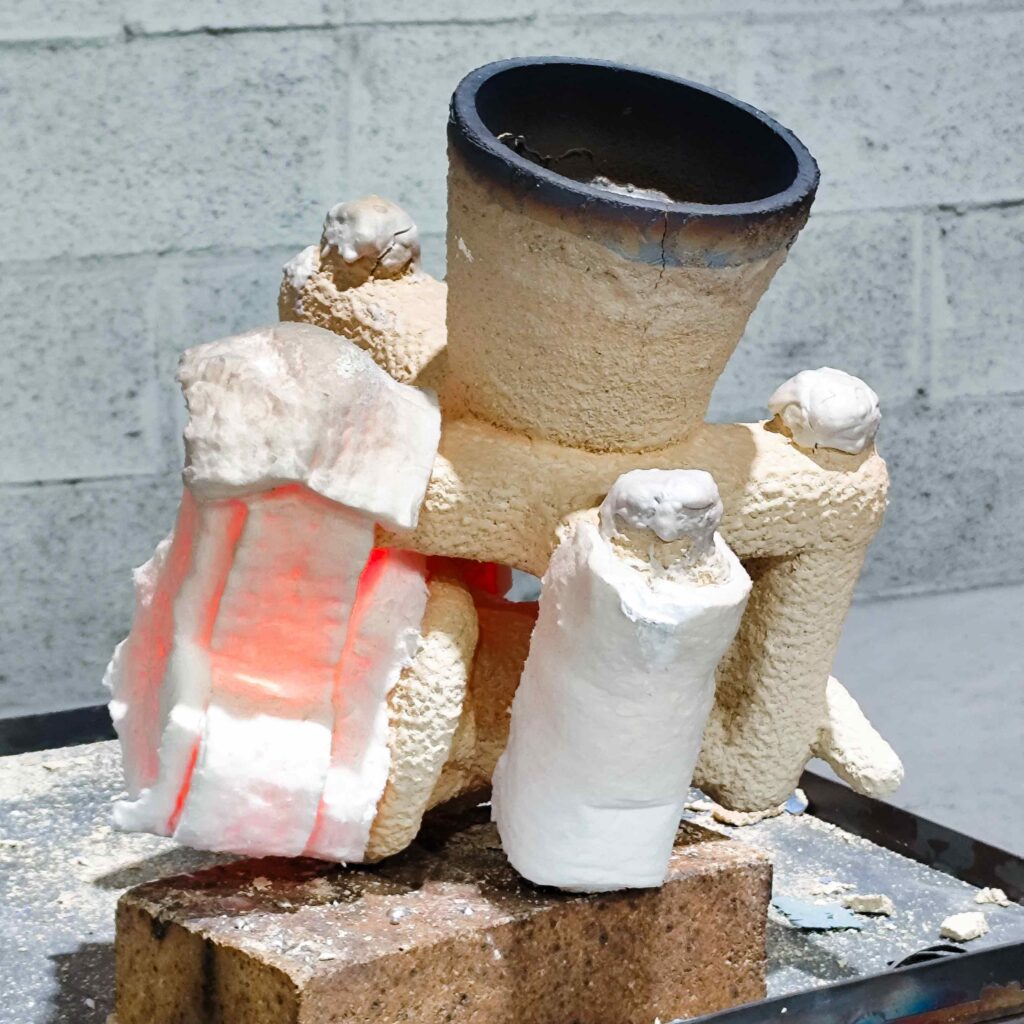
Casting in solidification and cooling process
The cooling rate affects:
- Grain Size: slow cooling allows the formation of larger crystalline grains, while faster cooling produces smaller, finer grains. Finer grains often result in better mechanical properties, such as higher strength and toughness.
- Thermal Gradients: A controlled thermal gradient ensures directional solidification, where the metal solidifies in a planned manner, from one end of the casting to the other.
STAGES OF THE SOLIDIFICATION PROCESS
Nucleation: Solidification begins with nucleation, the process by which the first solid crystals form in the liquid metal. There are two main types of nucleation:
Homogeneous nucleation: occurs spontaneously within the pure liquid.
Heterogeneous nucleation: Occurs in the presence of impurities or on the walls of the mould. In practice, heterogeneous nucleation is predominant in investment casting due to the interaction between the molten metal and the ceramic mould surface.
Subcooling and activation energy: Subcooling, the difference between the theoretical melting temperature and the actual temperature at which solidification begins, plays a crucial role in the initiation of solidification. The activation energy required for nucleation is directly related to the degree of subcooling.
Formation of the crystalline structure: Once the nuclei have formed, grain growth begins, forming the crystalline structure of the metal that will define the characteristics of the resulting metal part. This process is controlled by heat transfer and diffusion of atoms at the solid-liquid interface. The morphology of solidification can be:
Planar: Característica de velocidades de solidificación muy lentas y gradientes térmicos altos.
Cellular: Forms at intermediate solidification rates.
Dendritic: Typical of high solidification rates and low thermal gradients. In investment casting, dendritic morphology is the most common due to the typical solidification conditions of the process. Achieving the right balance between directional and equiaxial solidification patterns is crucial to optimise the mechanical properties of the casting.
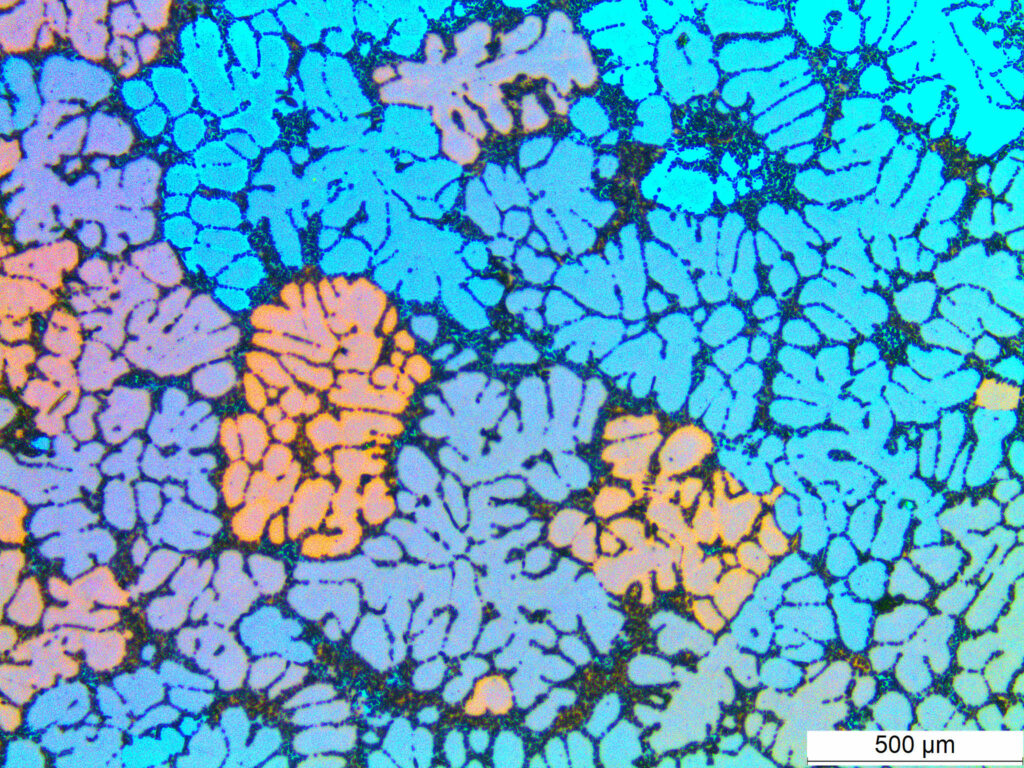
Equiaxial grain structure in an aluminium sample under polarised light
There are two main types of solidification patterns that can occur within the mould:
- Directional or Columnar Grain Growth: In directional solidification, grains grow perpendicular to the mould wall in a columnar pattern, usually encouraged by a controlled temperature gradient. This pattern can provide anisotropic properties, with increased strength in the direction of grain growth. Directional solidification is commonly used in investment casting to avoid defects such as porosity and ensure the part has a strong, uniform grain structure.
- Equiaxial Grain Growth: Occurs when nucleation occurs simultaneously throughout the volume of the molten metal. Equiaxial grains grow in all directions, usually resulting in smaller, more uniform crystals. This tends to provide isotropic properties, with uniform strength in all directions, but can introduce challenges such as an increased risk of porosity formation.
MAIN CHALLENGES AND STRATEGIES TO OPTIMISE SOLIDIFICATION IN INVESTMENT CASTING
The solidification process in microfusion casting is particularly prone to defect formation and presents us with challenges that manufacturers must address in order to produce high quality, defect-free parts. Poor solidification can lead to defects such as:
- Shrinkage: As the metal solidifies, it shrinks. If shrinkage is not adequately compensated for by adding more liquid metal, cavities or voids can form within the part (which we call ‘shrinkage’), leading to weaker areas in the casting.
- Porosity: Porosity occurs when gases are trapped in the molten metal during solidification. This can create voids or bubbles, reducing the overall density and strength of the part.
- Grain Structure Problems: The grain structure of the metal, which forms during solidification, directly impacts the mechanical strength, ductility and fatigue resistance of the part.
- Hot Cracking: This defect arises when the casting is subjected to thermal stresses during solidification, resulting in cracks or tears. This is especially problematic in alloys that have a long solidification range, where liquid and solid phases coexist for a longer time.
For these reasons, maintaining intensive control during the solidification process is vital to obtain components that meet dimensional, structural and mechanical requirements. Overcoming these challenges requires mastery of a combination of advanced techniques and technologies. We employ various strategies to optimise the solidification process and minimise defects:
Use of Simulation and Modelling tools
Simulation software has become an indispensable tool in the investment casting industry. By simulating the solidification process, manufacturers can predict potential defects, such as shrinkage or porosity, and make adjustments to mould design, pouring technique or cooling rate before actual casting begins. Software such as MAGMASOFT, ProCAST and FLOW-3D Cast can simulate thermal gradients, solidification front and defect formation during casting. These simulations help engineers identify areas where shrinkage or porosity may occur and optimise the mould design accordingly.
R&D applied to the development of improved alloys
Alloy composition significantly influences the onset of solidification. Alloys with a wide solidification range (difference between liquidus and solidus temperature) tend to have a more gradual solidification process than pure metals or eutectic alloys. Alloys designed specifically for investment casting can help mitigate some of the challenges associated with solidification.
Grain Tuners: Elements such as titanium, boron or zirconium can be added to the metal to promote grain refinement and improve the overall microstructure of the casting.
Mould and Process Design Optimisation
Mould design plays a crucial role in controlling the solidification process. By designing the mould to promote directional solidification and uniform cooling, manufacturers can reduce the risk of shrinkage, porosity and other defects.
Conclusion
The solidification process in investment casting is highly complex and determines the quality of the final part. Managing the complexities of this process requires careful attention to multiple parameters and a knowledge and mastery of all the manufacturing technologies involved in the investment casting process