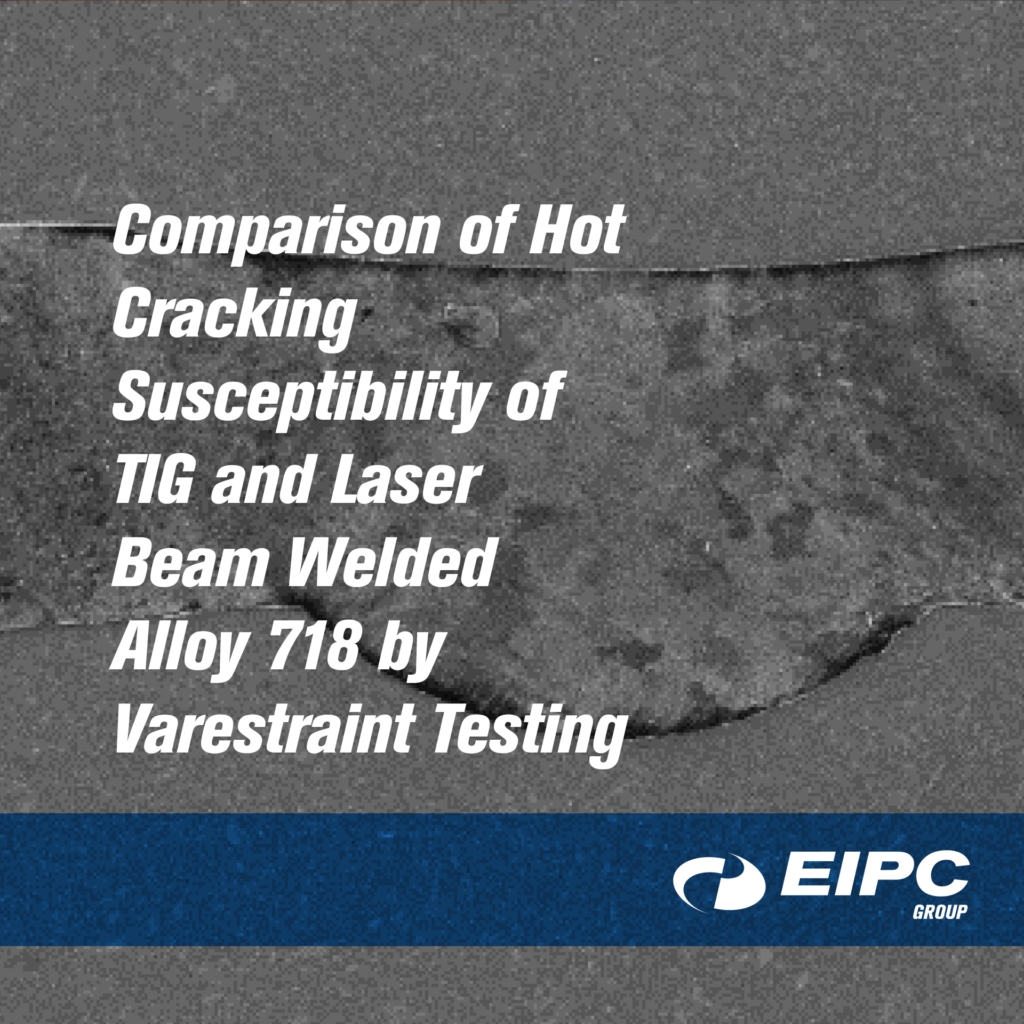
Comparison of Hot Cracking Susceptibility of TIG and Laser Beam Welded Alloy 718 by Varestraint Testing
This work addresses the hot cracking susceptibility of Alloy 718, a nickel-based superalloy widely used in aerospace applications, by comparing TIG (Tungsten Inert Gas) and LBW (Laser Beam Welding) methods through Varestraint testing. The study aims to better understand how welding conditions, material source (wrought or cast), and microstructural characteristics influence crack formation during solidification.
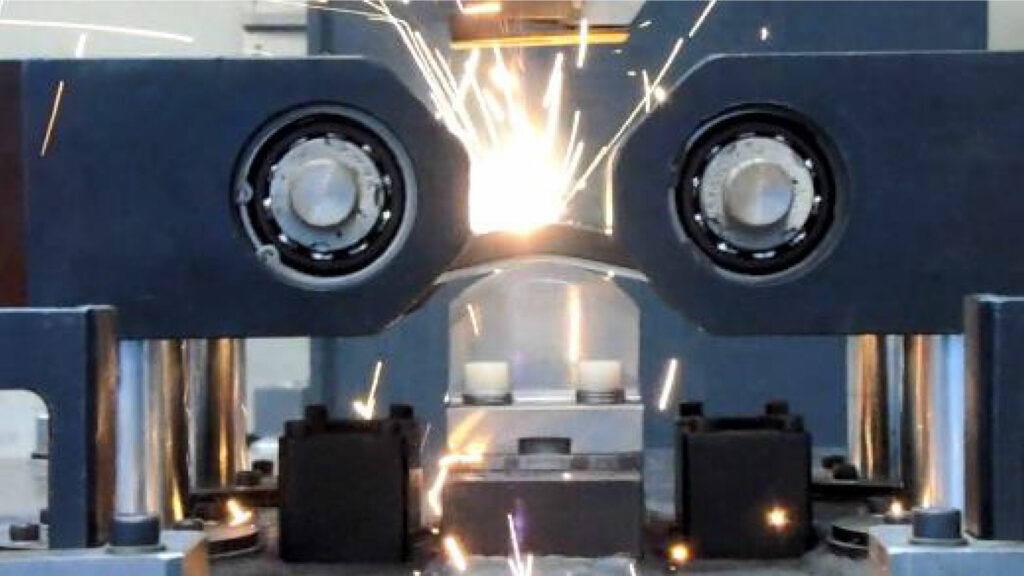
LBW Varestraint testing
Welding technologies comparison
TIG vs. LBW: Four welding conditions were evaluated (continuous TIG, pulsed TIG, continuous LBW, and pulsed LBW). Results showed that LBW welding is more susceptible to hot cracking due to “fishbone-like” solidification patterns, with extended centerline cracks in the fusion zone (FZ). Impact of pulsation: Although pulsation in both techniques slightly reduced cracking susceptibility, its effect was limited. Pulsation promoted a more uniform microstructure in some cases but did not prevent the formation of harmful intermetallic phases, such as the Laves phase.
Influence of microstructure and material source
Casting vs. wrought: Surprisingly, casting samples, despite having grain sizes 30 times larger than wrought samples, exhibited lower cracking susceptibility. This finding contradicts the common belief that finer grains improve weldability and suggests that other factors, such as secondary phase distribution and chemical composition, may play a decisive role.
Laves phase and Nb segregation: Heat-affected zones (HAZ) and fusion zones (FZ) showed significant niobium segregation and the formation of a continuous Laves phase network in the welded samples. These features were critical points for crack initiation and propagation.
Relevance to industrial applications
Welding parameters were optimized to meet strict industrial quality criteria, including full penetration, minimum weld width (>>1.5 mm), and the absence of surface defects. This approach ensures the practical applicability of the results in the aerospace industry.
The differences in cracking susceptibility between technologies and materials emphasize the need for careful selection of welding techniques and parameters based on specific application requirements.
Key conclusions
LBW, while offering advantages such as lower heat input and higher speed, is more prone to solidification cracking than TIG under the conditions studied. Investment casting can outperform wrought material in terms of weldability, even with coarser grains, challenging traditional notions about grain size impact. The Laves phase and Nb segregation are critical factors that must be minimized to enhance resistance to hot cracking.
This research, carried out in collaboration with the Azterlan and Lortek research centres, provides valuable insights to optimize the manufacturing of Alloy 718 components, particularly in critical applications where weldability and resistance to cracking are paramount. Access to the full text download HERE
- Post Tags:
- research
- White paper