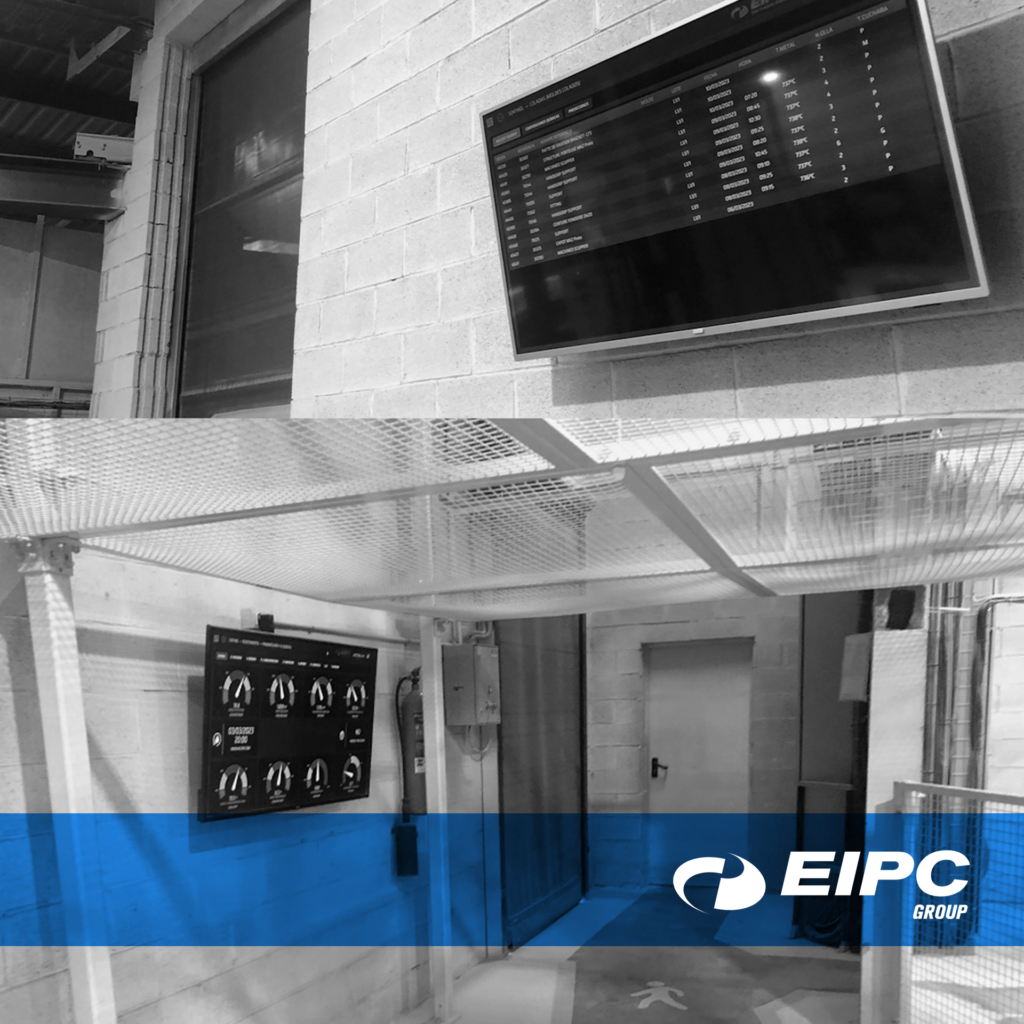
Scientific paper: Development of an artificial intelligence-based digital twin for rejection rate reduction and mechanical properties improvement in an investment casting plant
By Javier Nieves ,David Garcia, Jorge Angulo-Pines, Fernando Santos y Pedro Pablo Rodriguez
The manufacturing process carried out in the investment casting industry suffers from problems similar to other production processes. In addition, the high requirements of the customers and the industries that require these parts mean that high quality standards must be met. If those requirements are not achieved, this leads to the rejection of the manufactured parts. Therefore, given the current technology revolution (i.e., Industry 4.0) and the possibilities offered by tools such as digital twins and artificial intelligence, it is possible to work on the generation of intelligent systems that can reduce and even avoid these problems
Therefore, this study proposes the creation of a digital twin based on artificial intelligence to work on proactively identifying problems before they happen and, if they are detected, launch an optimization process that offers corrective actions to solve them. More specifically, this work focuses on the analysis of the manufacturing process (definition, KPI extraction, capture, distribution, and visualization), the creation of a base system for the integral management of process optimization, and experiments developed for determining the best method for making predictions. In this context, this research addresses two of the most critical defects:
- Porosity
- Mechanical properties
The approach is based on Industry 4.0 principles, using tools such as machine learning, simulation systems and predictive analytics to optimise manufacturing. Specifically, this work focuses on the analysis of the manufacturing process (definition, extraction of KPIs, capture, distribution and visualisation), the creation of a base system for the integrated management of process optimisation and the experiments developed to determine the best method for making predictions.
Firstly, work was done on improving the digitisation and representation of reality in a digital environment. A data analysis plan was followed which included:
- Identification of available data and data that, although initially not accessible, could be digitised and extracted at a later stage.
- Audit of the status of each area and its variables.
- Study of the impact and priority of the areas and their respective variables.
- Creation of a centralised data repository to store the information captured, using an agent-based system such as PDManager.
Subsequently, this data was to be used efficiently. It started with the creation of a low level of maturity digital twin, focused on remote visualisation and monitoring. Later, the digital twin evolved to a higher maturity level, moving from a reactive to a proactive approach. In this new stage, simulation and optimisation tasks were integrated, using supervised machine learning to make predictions.
Finally, based on the data collected and the predictions, a system was designed that proposes corrective actions in real time to optimise the process.
To read the full study, download HERE
You might also like
-
Ceramic coatings: the key role of the ‘shell’ material in lost-wax casting. https://www.eibarprecisioncasting.com/wp-content/uploads/2024/10/IMG_20241008_090630-768x1024.jpg 768 1024 Eibar Precision Casting Eibar Precision Casting https://www.eibarprecisioncasting.com/wp-content/uploads/2024/10/IMG_20241008_090630-768x1024.jpg