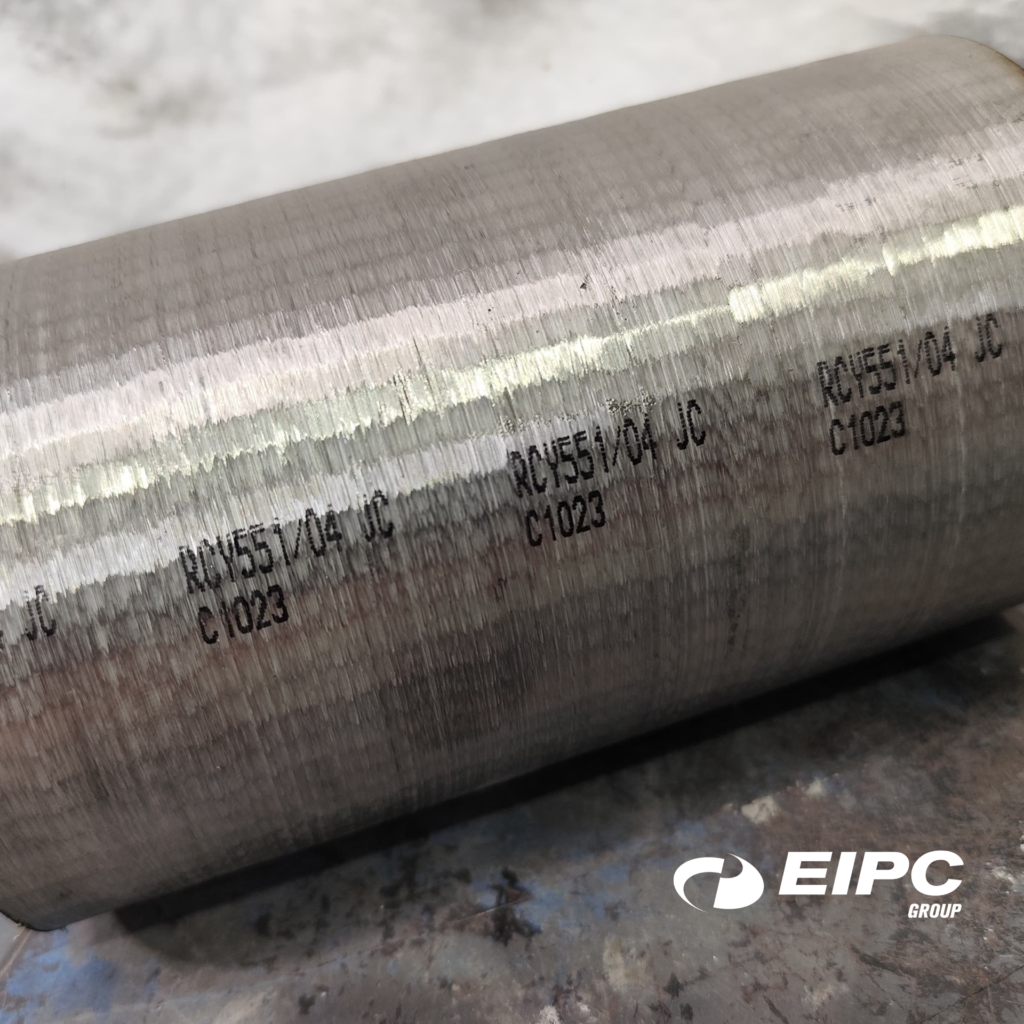
Alloy C1023 in the aerospace industry: case studies, issues, challenges and future challenges
Nickel alloys play a crucial role in industries that demand high-performance materials with exceptional mechanical strength and resistance in harsh environments. Among these, alloy C1023 has become an indispensable material for critical components in the aerospace industry. From turbine blades to exhaust systems, alloy C1023 ensures reliability in extreme conditions. This text explores real-world case studies, problem-solving challenges and key lessons learned from its application in the aerospace industry.
C1023, an alloy with outstanding properties
Alloy C1023 is an alloy of nickel, cobalt, chromium and molybdenum, carefully designed to improve mechanical and thermal performance. Its typical composition includes:
– Nickel (Ni): 50-55%.
– Chromium (Cr): 14-16%.
– Cobalt (Co): 9-10% Molybdenum (Mo): 7,5-9
– Molybdenum (Mo): 7.5-9% Molybdenum (Mo): 7.5-9%
– Aluminium (Al): 4
– Titanium (Ti): 3.5%
– Other elements (Fe, Si, Mn, W, Nb, etc.): <2%
The alloy is made by vacuum melting, which ensures high purity and a refined microstructure that enhances its mechanical properties. C1023 is known for its exceptional mechanical strength, corrosion resistance and thermal stability, making it an ideal choice for demanding aerospace applications.
Alloy C1023, aerospace industry applications
1 – C1023 in jet engine turbines
One of the most critical components in jet engines are the turbine assemblies, which must withstand extreme temperatures and mechanical stresses. In a recent study, aerospace engineers found that C1023 performed exceptionally well in high-temperature environments, maintaining its structural integrity and reducing oxidation-related failures. Over time, engines using C1023-based turbine components showed longer operating life and lower maintenance costs compared to traditional alloys.
One specific example involved a major airline that reported problems with turbine blade cracks in engines using traditional materials. After switching to C1023, they saw a 40% decrease in failure rates and a significant reduction in unscheduled maintenance, which improved engine efficiency and performance.
2 – High-temperature exhaust systems
Aircraft exhaust systems must withstand both thermal cycling and corrosive environments. A major aerospace manufacturer replaced traditional stainless steel exhaust components with C1023, resulting in increased durability and resistance to thermal fatigue. Flight data revealed a 30% increase in component longevity, leading to increased operational efficiency and reduced replacement costs.
In one documented case, a military aircraft unit discovered that previous exhaust materials were suffering from premature oxidation, leading to performance degradation. After adopting C1023, the aircraft experienced an 18-month increase in component life, reducing downtime and improving mission readiness.
3- Structural parts in hypersonic vehicles
With the rise of hypersonic flight, materials must withstand extreme aerodynamic forces and heat. C1023 was incorporated into the structural framework of an experimental hypersonic vehicle. Test flights confirmed that the high strength and oxidation resistance of the alloy prevented material degradation, even at speeds above Mach 5. These results underscored the alloy’s potential for future aerospace innovations.
Lockheed Martin, a defense contractor for the U.S. government working on a next-generation hypersonic missile, reported that the stability of C1023 allowed extended flight times without compromising the structure. This breakthrough demonstrated the material’s potential in future high-speed aviation and space exploration applications.
Problems in the use of alloy C1023 in the aerospace industry
Despite its advantages, integrating C1023 into aerospace applications presents significant technical challenges when working with this high-performance alloy. At both the engineering and management levels, C1023 is not without problems that require careful consideration when manufacturing components with this alloy.
1. Machining difficulties
Due to its high hardness, C1023 can be difficult to machine, leading to increased tool wear, longer production times and other related problems. To mitigate the risks inherent in machining, especially on highly competitive parts, alternative precision machining techniques, such as EDM and laser cutting, are being employed to improve efficiency, reduce material waste and minimize deformation risks.
2. Problems resulting from thermal expansion
In environments with rapid temperature fluctuations, differences in thermal expansion rates between C1023 and adjacent materials can lead to mechanical stresses. Aerospace engineers have developed hybrid component designs that incorporate damping layers to accommodate expansion mismatches, reducing the risk of stress fractures.
3. Cost Management
Nickel and cobalt are expensive raw materials, making C1023 an expensive option for large-scale production. However, advances in various advanced manufacturing technologies are leading to optimization in material usage, reducing waste and lowering overall production costs.
Lessons learned from C1023 implementations
Through extensive research and practical applications, the aerospace industry has gained several insights into optimizing the use of C1023:
- Material selection must be specific to each application. Although C1023 excels in high-temperature environments, it is not always the most cost-effective choice for components exposed to lower stresses. Engineers must balance performance requirements with budget constraints.
- Advanced manufacturing techniques improve efficiency. The use of the most suitable techniques in precision machining, microfusion, 3D printing and surface treatments can significantly improve the workability and service life of C1023 components.
- Materials research is essential. Continued investment in materials science can unlock further improvements in alloy performance, and thus make C1023 even more effective for next-generation aerospace applications.
Although challenges such as high cost and machining difficulties are major obstacles to working this strategic alloy, innovative solutions continue to improve its practicality. By studying real-world applications, solving common problems and applying lessons learned, the aerospace industry can maximize the benefits of C1023 and pave the way for future advances in aviation and space exploration.