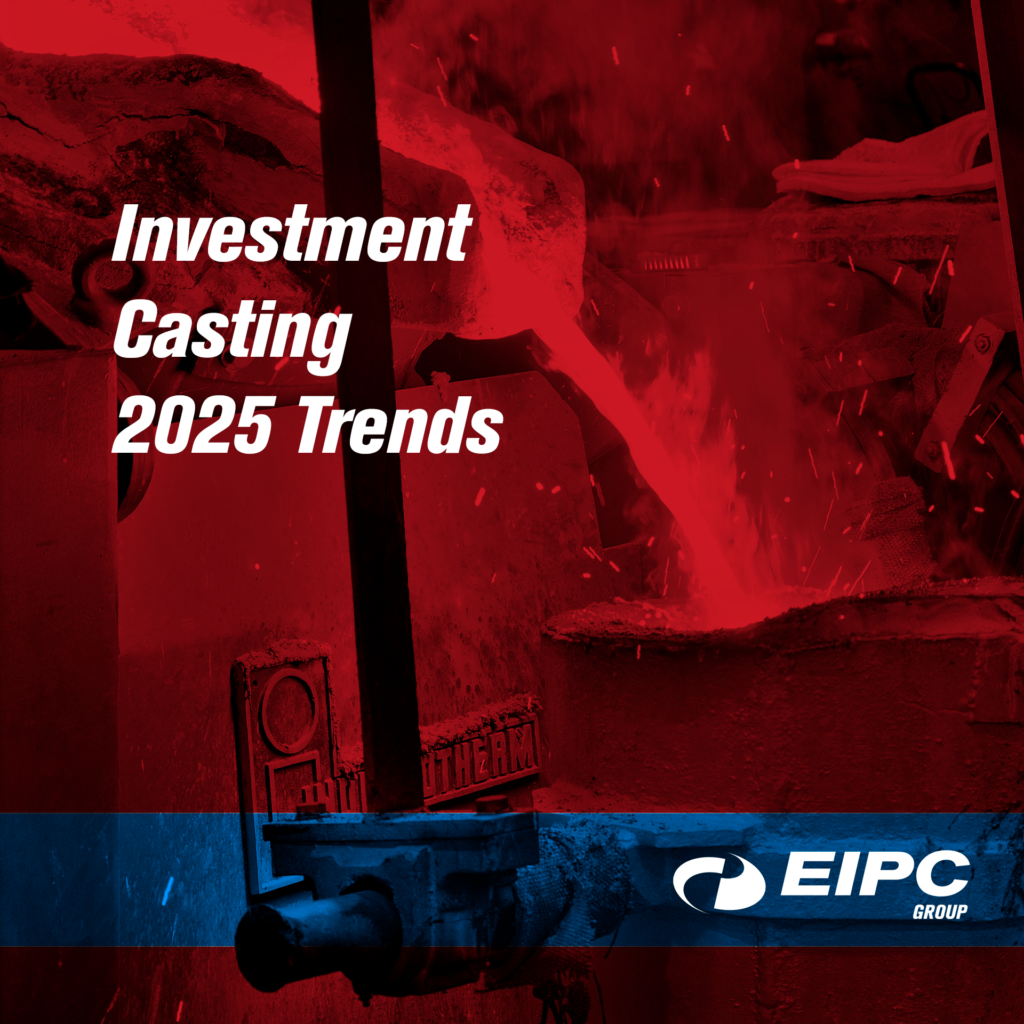
Investment Casting 2025 trends: Innovation and Economic Impact
Investment casting is an age-old technology that has evolved to become key to the production of high-precision metal parts used in sectors such as aerospace, automotive, medical and energy.
Thanks to the latest advances in innovation, this technology is advancing and making it possible to produce parts of ever greater technical complexity and mechanical characteristics.
Let’s take a look at what we can expect in 2025 in the sector.
Investment Casting 2025 trends: Technological Innovation
Research and development of advanced materials
The development of superalloys and new refractory materials is a prominent field in the evolution of casting technology. These materials enable the production of parts with superior mechanical properties and increased resistance to extreme temperatures, especially for aerospace and gas turbine applications. In addition, the latest advances in nanotechnology applied to ceramic coatings are focused on substantially improving the surface quality of final parts and reducing defects such as inclusions and porosity.
Integrated Additive Manufacturing (3D Printing)
3D printing is a technology that is transforming many industrial manufacturing processes, and microfusion is no exception. A concrete example of this is the integration of this technology in the design of wax models for the creation of ceramic moulds. The use of 3D printers to manufacture patterns directly reduces the pre-development times common in the microfusion process, improves design flexibility and reduces the initial costs associated with traditional tools and moulds
Automation and Artificial Intelligence (AI)
One of the ways of seeking maximum optimisation and efficiency is the application of AI integration tools in the casting process. Machine learning algorithms are beginning to be used to predict and prevent defects during casting, while automated control systems improve production consistency.
Advanced Cooling Technologies
Advances in controlled cooling technologies enable the achievement of optimal metal microstructures and the reduction of internal stresses. These innovations are particularly important for critical components in sectors such as aerospace. At EIPC, we have developed a proprietary High-Performance Sensorized Cooling technology for Aluminum Casting, achieving exceptional results in the production of components with high demands for the aerospace industry.
2025 Outlook: Global Economic Impact
Market Expansion
The growth of sectors such as renewable energy (particularly wind turbines) and electric mobility is driving the demand for components manufactured through investment casting. Additionally, the increasing adoption of this technology in emerging markets is fostering the globalization of the supply chain.
Sustainability and Circular Economy
The use of recyclable materials and more efficient processes is aligning with sustainability trends. Leading companies are investing in ceramic mould recycling techniques and reuse of waste materials, which contributes to reducing the sector’s carbon footprint.
Scientific Outlook and Challenges in 2025
Improved Quality Control
The development of non-destructive inspection technologies, such as computed tomography (CT) and advanced ultrasound, is improving the ability to detect internal defects in complex parts, increasing reliability in critical applications.
Digitalization and Simulation
Computer simulation is enabling more accurate predictions of material behavior during casting and solidification. Tools like digital twins offer innovative solutions to optimize designs and processes before physical implementation. Despite the advancements, significant barriers remain, such as the high initial costs of automation and the lack of global standardization in certain processes. Additionally, there is an ongoing need to train the workforce in handling new technologies.
Conclusion
In 2025, investment casting is at a turning point, driven by technological advancements such as additive manufacturing, automation, and advanced materials. These innovations are not only transforming the industry from a technical perspective but are also generating significant economic impact by reducing costs, improving sustainability, and expanding markets. However, the effective implementation of these trends will require overcoming technological and organizational barriers, as well as fostering global collaboration in research and development..