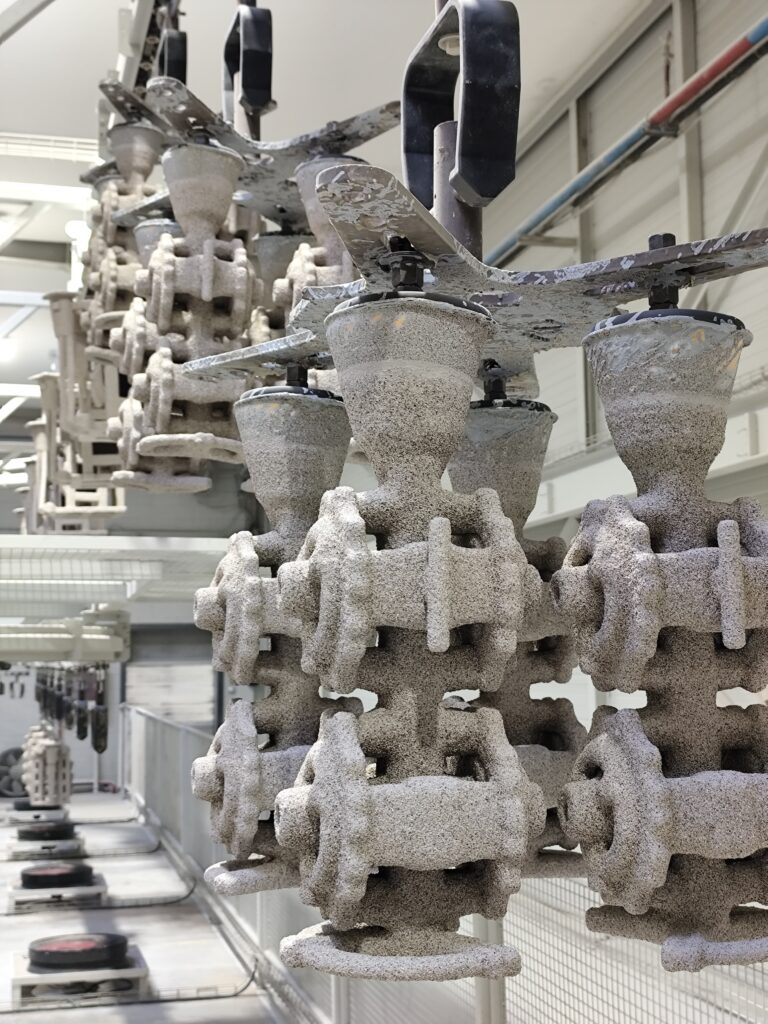
Ceramic coatings: the key role of the ‘shell’ material in lost-wax casting.
The creation of the ceramic mold for casting is one of the most complex and critical operations within the overall process of manufacturing metal parts by lost-wax casting. This ceramic coating process is carried out in our automated Shell-Room, the heart of the investment casting process, and is managed by the Shell-Room Manager, a fundamental position in our organization that coordinates and oversees the production of molds.
A deep understanding of materials technology and precise handling of ultra-specialized equipment to form the ceramic shell around the wax pieces are key factors to achieve maximum reliability and efficiency in the mold, tailored to work with each alloy that will be cast in the next step.
Let’s take a closer look at the importance of materials technology in the coating process.
MATERIALS TECHNOLOGY IN THE CREATION OF INVESTMENT CASTING MOULDS
In lost-wax casting, ceramic molds are formed by applying several layers of a ceramic slurry onto the wax model. These slurries are composed of different materials that provide strength and thermal stability. The coatings must withstand high temperatures, offer dimensional stability, and resist thermal shock. The main raw materials for ceramic coatings are:
Colloidal silica: This material is used as a binder in the slurries. It provides good thermal stability and is key to forming the ceramic layer. Ceramic flour: The refractory load of the slurries is composed of zirconium (zirconia), cobalt aluminate, fused silica, and aluminum silicates, materials that offer both mechanical strength and heat resistance.
Refractory sand: Aluminum oxide (alumina) and aluminum silicates are used as “stucco,” or coatings, which are progressively added in layers that evolve from fine to coarse grains, adding strength to the mold’s internal and external layers.
These raw materials, strategic for EIPC’s activities, are supplied by companies that ensure the highest quality worldwide, such as Ransom & Randolph, Remet, Imerys, Arciresa, Chilches, Midegasa, CCT, and many others.
1. Colloidal Silica (Main Binder))
Colloidal silica is the most commonly used binder in ceramic slurries. This material has a key function: providing cohesion to the ceramic particles that form the coating and giving structure to the mold. Colloidal silica is a suspension of small silicon dioxide (SiO2) particles in water, with particle sizes typically ranging from 5 to 25 nm. Its main properties are high thermal stability, great crack resistance, and easy handling.
- High thermal stability
- Colloidal silica maintains its structural properties at high temperatures, making it ideal for aerospace applications where high temperatures are required for casting metals such as superalloys.
- Crack resistance
- Due to the fineness of its particles, colloidal silica helps prevent cracks in the mold during drying or when the molten metal is poured.
- Easy handling
As a suspension, it is easy to apply and has good flow and dispersion properties. Additionally, viscosity can be adjusted depending on the application.
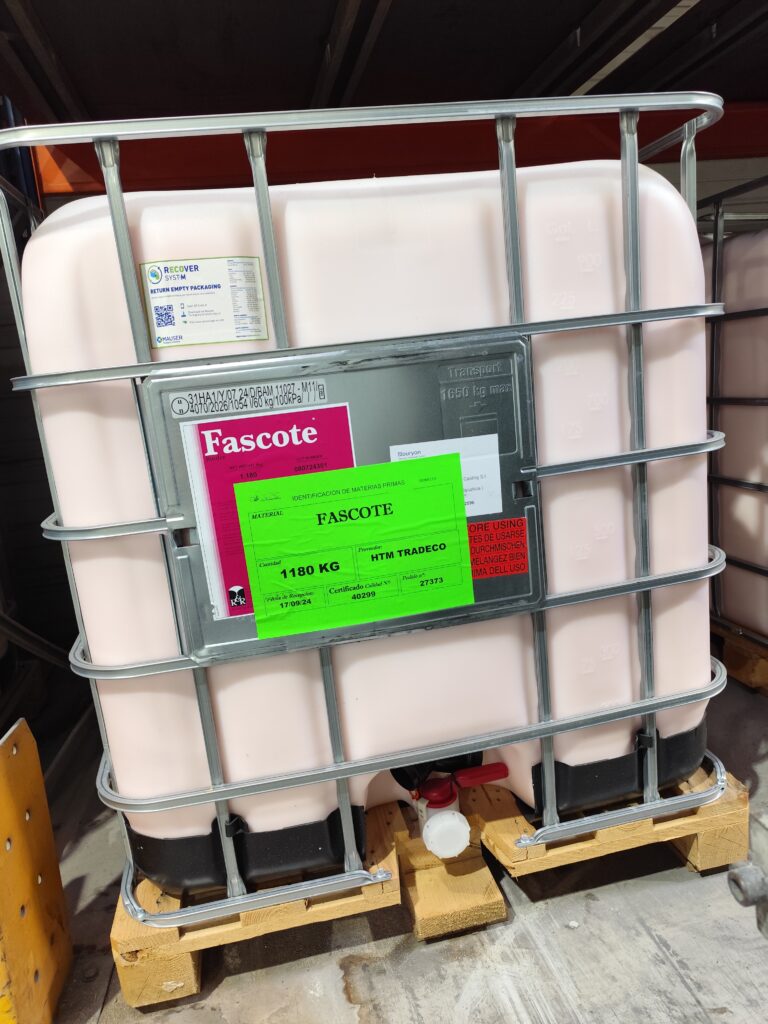
Colloidal Silica Fascote
The concentration of colloidal silica in the suspension must be carefully controlled to ensure a good balance between strength and flexibility. Temperature and humidity in the production environment can affect the stability of the suspension, so they must be carefully monitored.
2. Ceramic Flour (Refractory Material)
Ceramic flour provides structure and mechanical strength to the ceramic coating. This flour is mainly composed of refractory materials that can withstand high temperatures without degrading. At EIPC, we mainly use three types of ceramic flour:
- Zirconium (ZrO2):
Zirconium is a highly refractory material with an extremely high melting point, close to 2,715 °C. It offers excellent resistance to thermal shock, which is crucial when pouring very hot metals into the mold. Additionally, its low thermal conductivity helps control the metal’s solidification rate, improving the grain structure of the solidified metal.. - Cobalt Aluminate:
Used as a nucleating agent, it is added to the primary bath for molds where superalloys will be cast, helping control surface grain size and offering the best nucleation effect. - Fused Silica (SiO2):
Although silica has a lower melting point (around 1.600 °C), it remains a key component in ceramic coatings due to its flowability and compatibility with other refractory materials. It is mainly used in the inner layers of the mold, as its thermal stability is sufficient for the early stages of metal pouring.
- Aluminum Silicates with 60% Alumina content. Used for superalloys and steels.
Particle size of ceramic flour influences the mold’s strength and its ability to capture fine details of the wax model. Finer particles are used in the inner layers to improve the surface finish of the final part, while coarser particles are used in the outer layers to provide structural support.
3. Refractory Sand (Stucco)
Refractory sand, or stucco, is applied over the initial ceramic coating layers and backup layers. This material adds stiffness and strength to each layer of the mold, ensuring it can support the weight of the molten metal without deforming or breaking. Commonly used types of refractory sand include Alumina and Aluminum Silicates. Alumina (Al2O3): Alumina is one of the most widely used refractory materials due to its high temperature resistance and excellent thermal stability. It has a melting point of approximately 2,072 °C, making it ideal for casting advanced alloys. It provides high wear resistance and is suitable for molds that endure intense thermal cycles. Aluminum Silicates with variable Alumina content** (from 42% to 60%, depending on the metal to be cast and the size of the mold and parts). As with ceramic flour, the particle size of refractory sand is crucial. Larger particles are applied in the mold’s backup layers to provide adequate mechanical strength, while finer particles are used in intermediate layers to improve mold density
4. Processing Additives
Various additives are also used in ceramic slurries to improve the coating properties and optimize the application process.
- Viscosity modifiers: These are added to adjust the fluidity of the slurry. Controlled viscosity ensures good coverage of the wax model and prevents the formation of bubbles or uneven layers.
- Deflocculants: These additives help prevent the clumping of particles in the ceramic suspension, improving the coating’s homogeneity and stability.
- Biocides: Added to prevent the growth of bacteria in the suspension, which could alter the coating’s physical properties over time.
- Wetting agents: These additives improve the suspension’s ability to wet the wax model, ensuring uniform coverage, especially in complex or intricate areas.
Adding different types of resins or polymers to the Colloidal Silica formulations serves multiple purposes:
- Improve the adhesion of the first layer to the wax models, taking advantage of the binding properties of these resins or polymers.
- Provide elasticity to the first layer, so that potential variations in environmental conditions, such as faster drying or unexpected humidity changes, do not affect it as much, preventing cracking or peeling. It also improves the green strength of the ceramic mold, avoiding possible cracks caused by wax expansion during autoclave dewaxing.
- Being organic products, these additives burn off or disappear during the sintering of the ceramic mold, increasing the mold’s porosity and permeability, contributing to better filling of the cast parts.
Nowadays, most Colloidal Silica manufacturers provide the product ready to use, meaning it comes with defoamers, wetting agents, and resins or polymers already added.
The selection and control of raw materials in ceramic coatings are essential for mold quality and, ultimately, for the quality of the cast part.
At EIPC, we prepare customized coating formulations for each part we manufacture, ensuring that complex and high-value parts, such as those used in the aerospace industry, meet the strict standards of precision and quality.
You might also like
-
Scientific paper: Development of an artificial intelligence-based digital twin for rejection rate reduction and mechanical properties improvement in an investment casting plant https://www.eibarprecisioncasting.com/wp-content/uploads/2025/03/Gemelo-digital-basado-en-inteligencia-digital-portada-1024x1024.png 1024 1024 Eibar Precision Casting Eibar Precision Casting https://www.eibarprecisioncasting.com/wp-content/uploads/2025/03/Gemelo-digital-basado-en-inteligencia-digital-portada-1024x1024.png