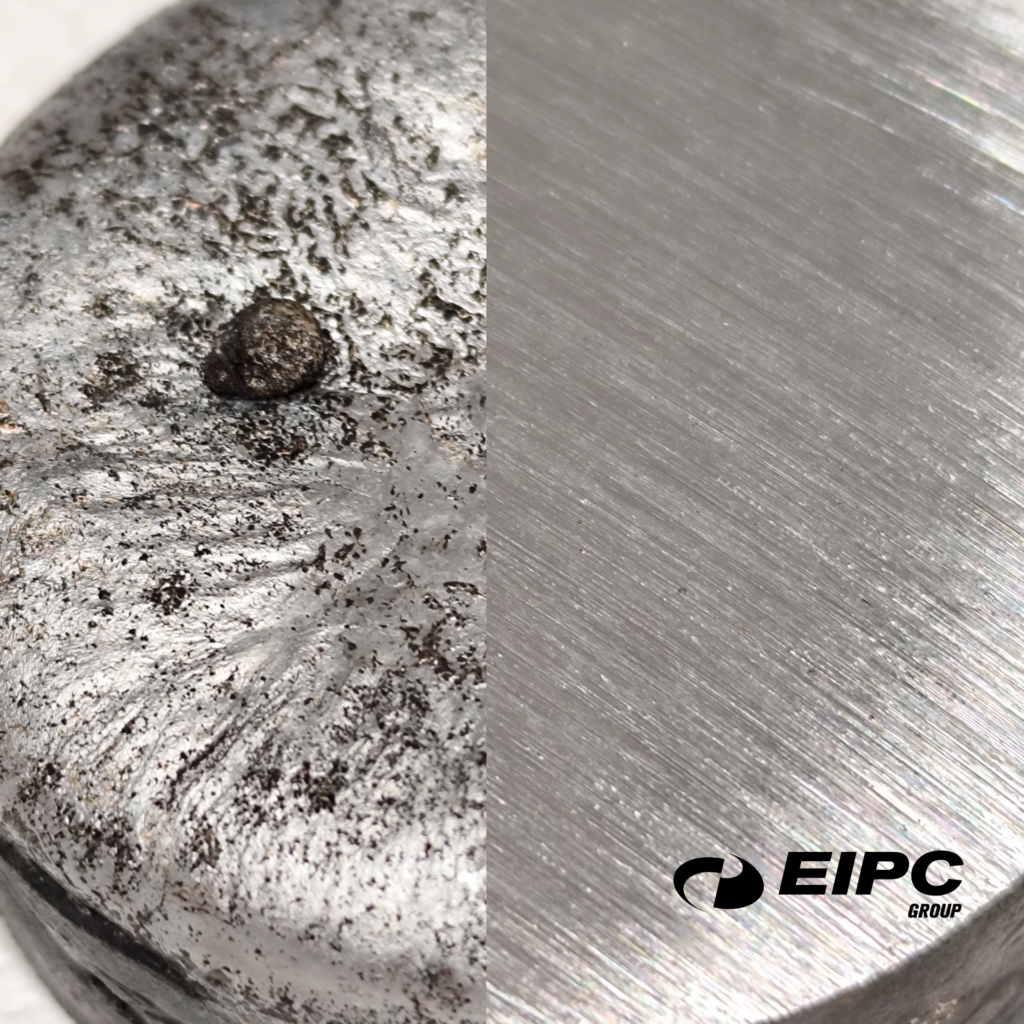
El proceso de solidificación en la industria de fundición a la cera perdida: hitos, factores clave y principales retos
La fundición a la cera perdida, también conocida como microfusión o investment casting, es una técnica de fabricación milenaria que ha evolucionado hasta convertirse en un proceso de alta precisión utilizado en diversas industrias, desde la aeroespacial hasta la joyería. En el corazón de este proceso de transformación de metales se encuentran los fenómenos de solidificación y contracción, cuya comprensión y control son fundamentales para la producción de piezas de alta calidad.
Vamos a poner el foco en los aspectos críticos de la solidificación y la compensación de la contracción en el proceso de microfusión. Analizaremos el inicio de la solidificación, la formación de la estructura cristalina, los métodos de control de la solidificación, y las estrategias para manejar la contracción y su compensación.
Fundamentos del proceso de solidificación en la industria de fundición a la cera perdida
La fabricación de un componente mediante el proceso de fundición a la cera perdida comienza con la creación de un patrón de cera que es una réplica exacta de la pieza final deseada. Este patrón se recubre con un material cerámico refractario que, al endurecerse, forma un molde preciso. La cera se derrite y se extrae del molde, dejando una cavidad que posteriormente se llenará con metal fundido.
El proceso de solidificación en la fundición a la cera perdida es una etapa clave en la conformación de la pieza, ya que influye directamente en la calidad final, la microestructura y las propiedades mecánicas de la misma. La solidificación implica la transición del metal fundido de un estado líquido a uno sólido dentro del molde cerámico, por lo tanto es un proceso térmico en el que el metal fundido pierde calor y comienza a cristalizar.
A medida que el metal se enfría, los átomos en la fase líquida comienzan a organizarse en una estructura cristalina, marcando la transformación de líquido a sólido. Esta transformación depende de varios factores, incluyendo el tipo de aleación metálica, la geometría del molde y la velocidad de enfriamiento.
TIPO DE ALEACIÓN
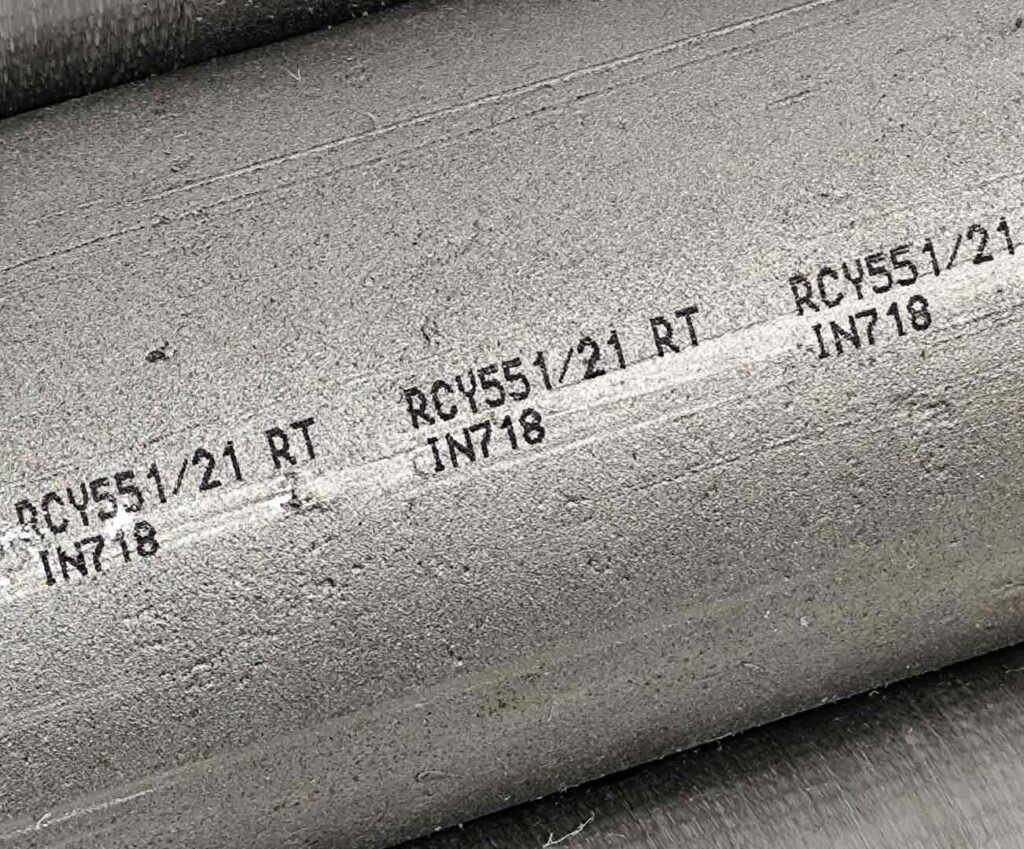
Detalle de lingote de aleación INCO 718
La elección de la aleación metálica desempeña un papel crucial en el proceso de solidificación. Diferentes aleaciones tienen distintos puntos de fusión y congelación, conductividades térmicas y tendencias a formar estructuras de grano específicas. Cada material tiene un perfil de solidificación único que influye en su comportamiento durante el enfriamiento y la cristalización. Los metales más comunes utilizados en la fundición a la cera perdida incluyen: Aleaciones de Aluminio, aleaciones de Acero y Súper aleaciones principalmente utilizadas en aplicaciones aeroespaciales debido a su capacidad para soportar temperaturas extremas.
GEOMETRÍA DEL MOLDE
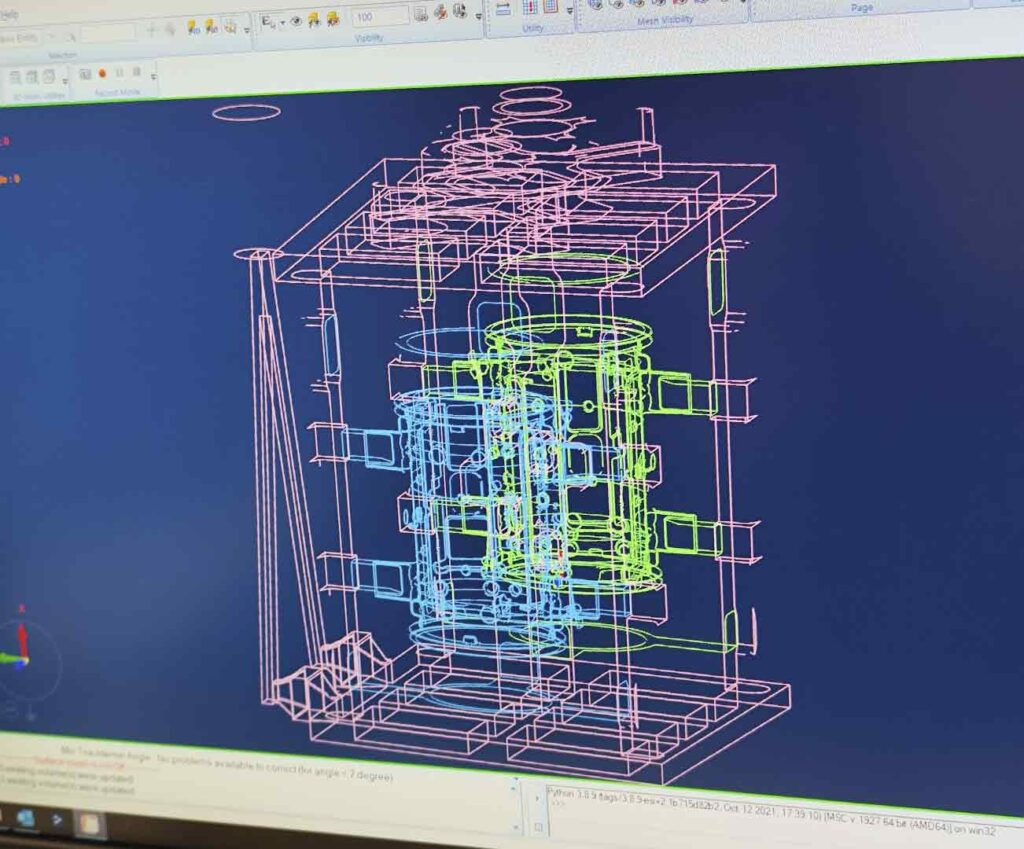
Diseño de molde para la obtención del positivo de pieza en cera
El diseño del molde cerámico afecta directamente a la forma en la que el metal fundido fluye y solidifica en su interior. Las principales consideraciones incluyen:
- Espesor de la Pared: El grosor de las paredes del molde impacta en la velocidad de enfriamiento del metal. Las paredes más gruesas generalmente ralentizan el enfriamiento, , mientras que las paredes más delgadas tienden a provocar enfriamientos más rápidos.
- Materiales del Molde: La composición del material del molde cerámico influye en sus propiedades térmicas. Una alta conductividad térmica en el material del molde puede llevar a un enfriamiento más rápido, lo que afecta la velocidad de solidificación y la microestructura resultante.
- Geometría de la Pieza Fundida: Las geometrías complejas pueden crear regiones donde el metal se enfría de manera desigual, lo que conduce a defectos localizados por contracción o a una solidificación incompleta.
VELOCIDAD DE ENFRIAMIENTO
La velocidad a la que el metal fundido se enfría y solidifica es crucial para el resultado de la pieza fundida, ya que pueden surgir defectos, como porosidad o rechupes si el proceso no se controla adecuadamente.
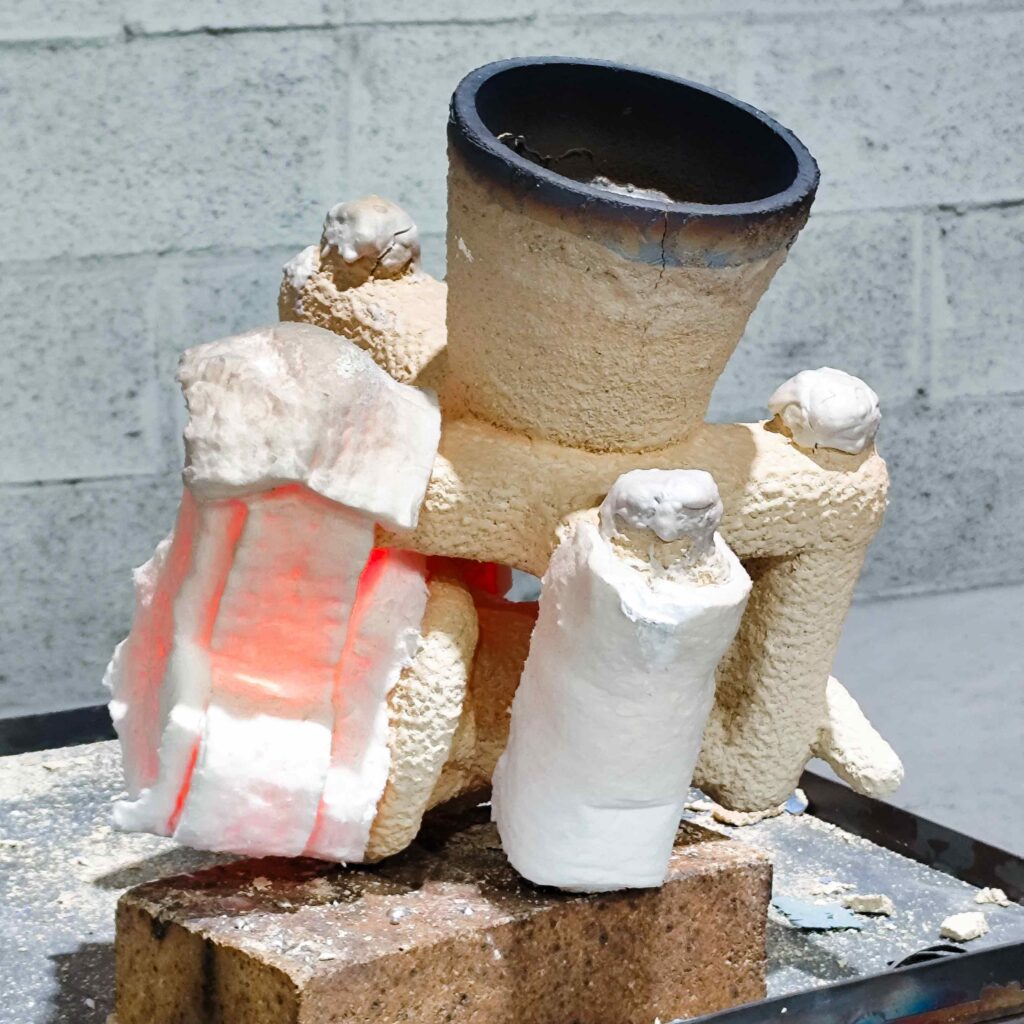
Colada en proceso de solidificación y enfriamiento
La velocidad de enfriamiento afecta a:
- Tamaño del Grano: Un enfriamiento lento permite la formación de granos cristalinos más grandes, mientras que un enfriamiento más rápido produce granos más pequeños y finos. Los granos más finos a menudo resultan en mejores propiedades mecánicas, como mayor resistencia y tenacidad.
- Gradientes Térmicos: Un gradiente térmico controlado asegura la solidificación direccional, en la que el metal solidifica de manera planificada, desde un extremo de la pieza fundida hacia el otro.
FASES DEL PROCESO DE SOLIDIFICACIÓN
Nucleación: La solidificación comienza con la nucleación, el proceso por el cual se forman los primeros cristales sólidos en el metal líquido. Existen dos tipos principales de nucleación:
Nucleación homogénea: Ocurre espontáneamente dentro del líquido puro.
Nucleación heterogénea: Se produce en presencia de impurezas o en las paredes del molde.
En la práctica, la nucleación heterogénea es predominante en la fundición a la cera perdida debido a la interacción entre el metal fundido y la superficie del molde cerámico.
Subenfriamiento y energía de activación: El subenfriamiento, la diferencia entre la temperatura de fusión teórica y la temperatura real a la que comienza la solidificación, juega un papel crucial en el inicio de la solidificación. La energía de activación necesaria para la nucleación está directamente relacionada con el grado de subenfriamiento.
Formación de la estructura cristalina: Una vez que se han formado los núcleos, comienza el crecimiento de los granos, formándose la estructura cristalina del metal que definirá las características de la pieza metálica resultante. Este proceso está controlado por la transferencia de calor y la difusión de átomos en la interfaz sólido-líquido.
La morfología de la solidificación puede ser:
Planar: Característica de velocidades de solidificación muy lentas y gradientes térmicos altos.
Celular: Se forma a velocidades de solidificación intermedias.
Dendrítica: Típica de altas velocidades de solidificación y bajos gradientes térmicos.
En la fundición a la cera perdida, la morfología dendrítica es la más común debido a las condiciones de solidificación típicas del proceso. Lograr el equilibrio adecuado entre los patrones de solidificación direccional y equiaxial es crucial para optimizar las propiedades mecánicas de la pieza fundida.
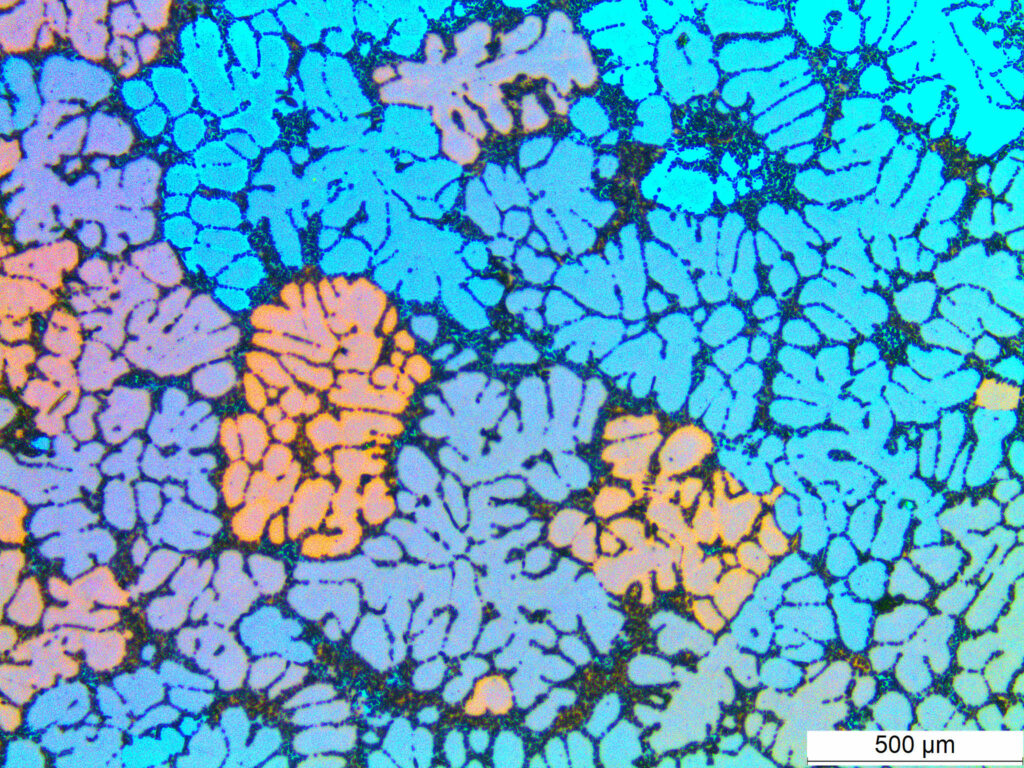
Estructura de grano equiaxial en una muesta de aluminio bajo luz polarizada
Existen dos tipos principales de patrones de solidificación que pueden ocurrir dentro del molde:
- Crecimiento de Grano Direccional o Columnar: En la solidificación direccional, los granos crecen perpendicularmente a la pared del molde en un patrón columnar, generalmente fomentado por un gradiente de temperatura controlado. Este patrón puede proporcionar propiedades anisotrópicas, con una mayor resistencia en la dirección del crecimiento del grano. La solidificación direccional es comúnmente utilizada en la fundición a la cera perdida para evitar defectos como la porosidad y garantizar que la pieza tenga una estructura de grano fuerte y uniforme.
- Crecimiento de Grano Equiaxial: Se da cuando la nucleación ocurre en simultáneamente en todo el volumen del metal fundido. Los granos equiaxiales crecen en todas las direcciones, lo que suele resultar en cristales más pequeños y uniformes. Esto tiende a proporcionar propiedades isotrópicas, con una resistencia uniforme en todas las direcciones, pero puede introducir desafíos como un mayor riesgo de formación de porosidad.
PRINCIPALES DESAFÍOS Y ESTRATEGIAS PARA OPTIMIZAR LA SOLIDIFICACIÓN EN MICROFUSIÓN
El proceso de solidificación en la fundición por microfusión es particularmente propenso a la formación de defectos y nos plantea desafíos que los fabricantes debemos abordar para producir piezas de alta calidad y sin defectos. Una mala solidificación puede llevar a defectos como:
- Contracción: A medida que el metal se solidifica, se contrae. Si la contracción no se compensa adecuadamente con la aportación de más metal líquido, pueden formarse cavidades o vacíos dentro de la pieza (que nosotros llamamos «rechupes»), lo que provoca áreas más débiles en la pieza fundida.
- Porosidad: La porosidad ocurre cuando los gases quedan atrapados en el metal fundido durante la solidificación. Esto puede crear vacíos o burbujas, reduciendo la densidad general y la resistencia de la pieza.
- Problemas con la Estructura de Grano: La estructura de grano del metal, que se forma durante la solidificación, impacta directamente en la resistencia mecánica, ductilidad y resistencia a la fatiga de la pieza.
- Grietas en Caliente: Este defecto surge cuando la pieza fundida está sometida a tensiones térmicas durante la solidificación, lo que provoca grietas o desgarros. Esto es especialmente problemático en aleaciones que tienen un rango de solidificación largo, donde coexisten fases líquidas y sólidas durante más tiempo.
Por estos motivos, mantener un control intensivo durante el proceso de solidificación es vital para obtener componentes que se ajusten a los requerimientos tanto dimensionales como estructurales y mecánicos. Superar los desafíos que se plantean requiere del dominio de una combinación de técnicas y tecnologías avanzadas.
Empleamos varias estrategias para optimizar el proceso de solidificación y minimizar los defectos:
Uso de herramientas de Simulación y Modelado
El software de simulación se ha convertido en una herramienta indispensable en la industria de la fundición a la cera perdida. Al simular el proceso de solidificación, los fabricantes podemos predecir posibles defectos, como los rechupes o la porosidad, y realizar ajustes en el diseño del molde, la técnica de vertido o la velocidad de enfriamiento antes de comenzar la fundición real.
Programas como MAGMASOFT, ProCAST y FLOW-3D Cast pueden simular los gradientes térmicos, el frente de solidificación y la formación de defectos durante la fundición. Estas simulaciones ayudan a los ingenieros a identificar áreas donde pueden ocurrir contracciones o porosidades y optimizar el diseño del molde en consecuencia.
I + D + I aplicada al desarrollo de aleaciones mejoradas
La composición de la aleación influye significativamente en el inicio de la solidificación. Las aleaciones con un rango de solidificación amplio (diferencia entre la temperatura de liquidus y solidus) tienden a tener un proceso de solidificación más gradual que los metales puros o las aleaciones eutécticas. Las aleaciones diseñadas específicamente para la fundición a la cera perdida pueden ayudar a mitigar algunos de los desafíos asociados con la solidificación.
Afinadores de Grano: Elementos como titanio, boro o circonio se pueden agregar al metal para promover el afinado del grano y mejorar la microestructura general de la pieza fundida.
Optimización en el Diseño de Moldes y Procesos
El diseño del molde juega un papel crucial en el control del proceso de solidificación. Al diseñar el molde para fomentar la solidificación direccional y el enfriamiento uniforme, los fabricantes pueden reducir el riesgo de rechupes, porosidad y otros defectos.
Conclusión
El proceso de solidificación en la fundición a la cera perdida es altamente complejo y determina la calidad de la pieza final. La gestión de las complejidades del mismo requiere una atención cuidadosa a múltiples parámetros y un conocimiento y dominio de todas las tecnologías de fabricación implicadas en el proceso de microfusión.